Montgomery College Student Services Center
Rockville, MD | e-Studio Site
Casey Zarger | Mechanical
Advisor: Dr. James Freihaut
GENERAL BUILDING DATA
Building name:
Building site:
Building occupant:
Building function:
Size:
Height:
Number of stories:
Dates of construction:
Project cost:
Project delivery method:
Montgomery College Student Services Center
51 Mannakee Street, Rockville, MD 20850
University office building
office space
128,000 gsf
81’
5 levels (5 floors & basement)
3-20-17 to 3-8-19
$55 Million (total cost)
design-bid-build (single prime contract)
Owner:
Owner’s representative
Prime consultant:
Associate architect:
Structural engineer:
MEP engineer:
Civil engineer:
Landscape architect:
AV/IT acoustics:
Fire protection and security:
Cost estimator:
Geotechnical engineer:
Hardware consultant:
Exterior envelope consultants:
Systems commissioning agent:
Montgomery College
Mr. Jamie Karn
Cho Benn Holback + Associates, Inc
Bohlin Cywinski Jackson
A & F Engineers, Inc
James Posey Associates
A Morton Thomas and Associates, Inc
Michael Vergason Landscape Architects
The Sextant Group, Inc
GHD
DMS Construction Consulting Services
Schnabel Engineering Consultants, Inc
Erbschloe Consulting Services, Inc.
Wiss Janney Elstner, Inc
Facility Dynamics Engineering Corp.
PROJECT TEAM
ARCHITECTURE
Design & functional components:
The Student Services Center is being designed and constructed by Montgomery College to replace its existing facility. The new building will house various student services, intake functions and programs serving students. It will also contain one academic department (school of education), administrative offices, the campus security office and a central plant operation serving both this building and the campus. The proposed building will consist of four stories above grade and a basement, and will contain 70,227 nsf and 128,004 gsp. The mechanical equipment will be located on the roof and in the basement. Each department is located within the building such that they remain a cohesive unit on the same floor and near other departments that work together. An emphasis was put on making the space inviting and easy to navigate for students. A large atrium on the first floor has a welcome center to aid students with questions and direct them to whatever department they’d like to visit. The building will be located at the end of the mall that runs the NS length of the campus. Glazing on the southern exterior will create an appealing gateway to the campus.
Montgomery College Design Standards (MCDS)
Montgomery College Energy Design Guidelines
2012 International Building Code (IBC)
2012 International Mechanical Code (IMC)
2012 International Energy Conservation Code (IECC)
National Electrical Code (NEC), NFPA 70 (latest edition)
Life Safety Code, NFPA 101
National Fire Protection Association Code (NFPA), NFPA 72
Maryland Building Performance Standards COMAR 05.02.07
Maryland Building Rehabilitation Code COMAR 05.16.01
State of Maryland Fire Prevention Code COMAR 29.06.01
Applicable codes:
Building envelope:
The masonry walls will be rain screen construction consisting of 4” masonry veneer, 4” cavity, 2” rigid insulation; air/water barrier and 8” CMU back up. The north, east and west brick veneer will match the brick on the Science Center. The brick on the southern elevation will be a lighter color complimentary to the other brick. Mineral wool batts within the stud cavity and/or rigid insulation in the air cavity will provide insulation.
The glazing system will consist of 1” insulated glazing units held in thermally-broken glazed aluminum curtainwall frames. High performance clear glass, with low-e coatings, will be used in most of the openings; opaque and translucent glass panels will be used in select locations. Operable windows with opening limits will be used in all offices.
Roofing will be constructed according to Montgomery College’s standard bituminous built-up roof, consisting of a high albedo cap sheet, 2-plies of modified bitumen membrane over a self-adhering base layer, cover board and R-25 rigid polyisocyanurate insulation. Stainless steel flashing will be used for transitions. An extensive green roof assembly will be installed at the second floor as indicated on the drawings. A tray system of sedum vegetation will be installed on top of the standard built-up roof.
The Energy Code will establish minimum design and performance criteria for the thermal characteristics of the building envelope assemblies. Masonry wall systems will incorporate a continuous cavity between the brick/panel veneer and the insulated backup wall, with a system of weeps to collect and drain any infiltrating moisture out of the wall. The cavity face of the substrate will be covered by a continuous air/water barrier.
Curtainwall insulation at spandrel conditions will be accomplished using mineral wool insulation between the interior finish and the curtain wall assembly. Sealants will be selected on the basis of performance, substrate material, and economy, and are expected to include both silicon and urethane based materials. A waterproofing system compatible and continuous with the air-water barrier system will be provided at below-grade conditions.
PRIMARY ENGINEERING SYSTEMS
Montgomery College Student Center construction is scheduled to begin in March of 2017 and finish in March of 2019. The project is being delivered using the design-bid-build method. The general contractor will be selected by Montgomery College and will be engaged as Contractor for this project. Building information modeling (BIM) is being utilized throughout the process to facilitate design and construction.
Construction:
Normal power for the entire building will be provided by a 3000-amp main fused bolted pressure switch with copper bus structure, as well as surge protection and integral owner metering. Branch panelboards will be either 480Y/277 volt or 208Y/120 volt with main circuit breakers, copper bus structure, and bolt-on type branch breakers. Branch circuit panelboards will feed lighting receptacle, and equipment loads. During unoccupied conditions, half of the receptacles in the offices and computer classrooms will automatically switch off.
Dry-type transformers will be served with 208Y/120 volt, 3-phase,4-wire secondary distribution. Branch circuit panelboards and dry-type transformers will be placed throughout the building. All three-phase motor loads will be provided with variable frequency drives. Conductors will be copper and installed within conduit.
Electrical:
An energy efficient lighting and control system will be specified for the building; lighting fixtures will be both fluorescent and LED. General lighting will operate at 277 volts in order to minimize the number of branch circuits. Most spaces, including classrooms, conference rooms, and offices, will utilize fluorescent fixtures with 25-watt, T5 linear fluorescent lamps and programmed start electronic ballasts. They will also employ ceiling-mounted occupancy sensors with 360-degree detection. Decorative lighting or point sources will be specified in lobbies, the atrium and other public areas. LED lights will be installed in interior locations where appropriate. Areas with open ceilings, such as mechanical rooms, electrical rooms, and storage rooms, will have 4-foot long chain suspended industrial-type fluorescent lighting fixtures. Stairwell lighting will have recessed, 2x4 high-efficiency fluorescent fixtures with occupancy sensors.
A daylight harvesting system will be used to reduce the energy consumption of the lighting system. Exterior lighting will be controlled by an automatic lighting control system with an astronomic time clock. Emergency power branch circuits will provide power to emergency egress lighting throughout the building.
Lighting:
The heating water will be supplied by a new boiler plant with five high-efficiency condensing boilers, with an additional two boilers for redundancy, based on the AERCO BMK-6000 boilers. The boiler plant will be located in the basement mechanical room. The heating plant will have a dedicated primary, variable secondary, and variable tertiary system. Inline primary pumps for each boiler are anticipated. Three pumps sized for 50 percent of the flow will serve the secondary campus side, while three additional pumps sized at 50 percent of the flow will serve the tertiary pumps for the building. The new campus heating water system is anticipated to match the existing campus supply and return temperatures; 170 degrees F heating water supply, and 140 degrees F heating water return.
Campus chilled water is currently generated and distributed in the basement of the Humanities building. The chilled water for the Student Services Center will be supplied by two new water cooled chillers and cooling towers. These satellite chillers will be located in the Student Services Center’s basement mechanical room, while the cooling towers will be located on the roof. The chillers will be based upon the Daiken Maglev Centrifugal chiller with variable frequency drive.
Two variable air volume air handling units will serve the Student Services Center. They will be equipped with 2-inch flat MERV 8 pre-filters, 12-inch cartridge type MERV 13 final filters, heating water preheat coils, chilled water cooling coils, and direct-drive plenum-type supply and return fans.
Single-duct VAV supply air terminal units with hydronic heating coils are anticipated for providing both space temperature and ventilation control for the building. A dedicated VAV terminal unit will be provided for each classroom, adjunct suite, conference room, corner office, department chair office, and specialty spaces. A single VAV terminal unit will support three or more interior offices, or perimeter offices with a common exposure. Dedicated and redundant ductless split systems and VAV terminal units will serve elevator machine rooms, IT rooms, and security closets.
Mechanical:
Structural:
The building is a mix of administrative offices and educational spaces, but will be designed as an institutional-grade office building in order to provide flexibility for future layout modifications.
The building will consist of structural steel framing on all floors. This system consists of concrete filled composite deck slabs supported by steel beams, girders, and steel columns. The concrete deck shall be reinforced with WWF and mild reinforcing over the steel beams and girders. The steel beams and girders are designed with steel studs to develop composite action with the concrete slab. Normal weight concrete will be used in the slabs on the composite steel deck due to lightweight concrete moisture content taking longer to drop to acceptable levels for finishing. Steel braces will be provided in both directions for the lateral stability of the building and resistance to wind and seismic forces. Two braces in each direction will be required. The typical brace would be an X pattern, with HSS 6x6x1/2 diagonal members.
Ground floor framing will be the same as the typical framing for the above ground floors. Basement walls will be 14” thick cast in place reinforced concrete walls, and the slab will be a 6” thick cast in place slab on grade on top of a 15 mil vapor retarder and 6” of free-draining granular fill. 6x6-W2.9xW2.9 WWF reinforcing will be provided in the SOG. The reinforcing in the loading dock slab shall be epoxy coated.
ENGINEERING SUPPORT SYSTEMS
Fire protection:
Montgomery College Student Services Center will be provided with a combined sprinkler/standpipe system for the entire structure, including a complete automatic wet-pipe sprinkler protection system with quick response sprinklers. No flexible piping is allowed in the building. The standpipe system will have hose connections at intermediate stair landings, or as otherwise required by local regulations. The combined system shall be supplied by the local campus water loop. If required, a pre-action sprinkler system shall be provided for the elevator shaft, and be released by the main building fire alarm control panel. All automatic sprinkler systems will be monitored by the fire alarm system.
Complete fire alarm and mass notification coverage will be provided in the building. ADA-compliant strobes, audible speakers, and text message boards will also be utilized. Emergency power and protection equipment will be provided to support fire protection requirements.
Transportation:
Four elevators serve the building, and each one is equipped with a sump pit. Two central elevators serve the main lobby and atrium and travel the height of the building, one western elevator serves the loading dock and travels between the basement and first floor, and one southern elevator serves the student life area and travels between the basement and first floor.
Three main stairwells serve the building, one on the east side of the building, one on the west side, and one on the south side. In addition, there is a large staircase that travels between the first and second floors within the atrium.
Two separate 8-way telecommunications duct bank extensions will be provided within North Campus Drive directly adjacent to the water main extension work, these extensions will include the construction of two new telecommunications manholes. Additionally, 4- way duct banks will be provided to connect the Technical Center and the new Student Services building on the west side as well as the Humanities building and the new Student Services building on the south side. There are currently underground telecom services running through the parking lot on the south side and the west side running from a point north of North Campus Drive. At this time both duct banks are proposed to be either removed or abandoned. Additionally, there is currently an overhead telephone line running through the west side of Lot 4 from a pole on the north side of North Campus Drive to a pole adjacent to the northeast corner of Humanities.
Telecommunications:
The emergency power generation system will include one emergency generator and provisions for a second emergency generator. The generator will provide emergency power to life safety loads and standby loads. Life safety loads include the fire pump, emergency egress lighting and signage, and the fire alarm and detection system. Optional standby loads will include all MDF and IFD closets and associated mechanical systems. The generator will be diesel fueled with and integral fuel storage tank and sound attenuated enclosure. The generator’s anticipated size is 200KW (stand-by rating).
The building will also include an electronic security system. It will connect to the existing Montgomery College Information Technology Facility Network.
Special systems:
Montgomery County Regulations
Zoning requirements:

Mechanical Room Floor Plan -
Courtesy of James Posey Associates

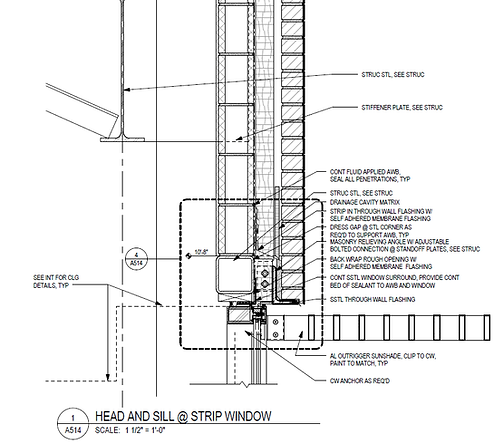
Parapet Wall Section -
Courtesy of James Posey Associates
Wall & Window Section -
Courtesy of James Posey Associates


North Facade Rendering - Courtesy of Bohlin Cywinski Jackson
​
North East Facade Rendering - Courtesy of Bohlin Cywinski Jackson
​

West Facade Rendering - Courtesy of Bohlin Cywinski Jackson
​

High-efficiency condensing boilers will be included in the design. An energy efficient lighting and control system will be specified, consisting of both fluorescent and LED fixtures. Occupancy sensors and a daylight harvesting system will reduce the energy consumption of the building. No large sustainability features, such as a green roof or solar panels, will be specified.
Sustainability Features: